Driving into the Future The Evolution of Electric Vehicle Design
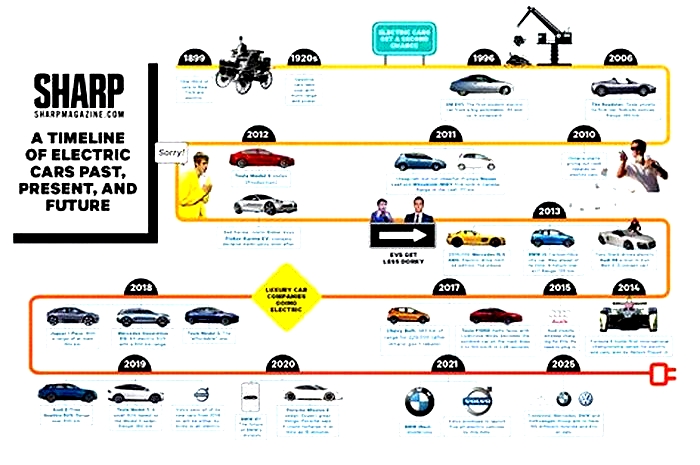
Trends in electric-vehicle design
Regulatory pressures on internal combustion engines (ICEs), combined with technological improvements in electric powertrains and batteries, are driving a surge of demand for electric vehicles (EVs). Most incumbent car manufacturers are rolling out models, joined by new entrants without ICE legacies. Worldwide sales of pure battery EVs (excluding hybrids) grew by approximately 45 percent in 2016.
Stay current on your favorite topics
With EVs becoming mass-market products, it is time for a detailed understanding of technology trends. In collaboration with A2Mac1, a provider of automotive benchmarking services, we conducted a large-scale benchmarking of first- and second-generation EV models, which included physically disassembling ten EV models: the 2011 Nissan LEAF, the 2013 Volkswagen e-up!, the 2013 Tesla Model S 60, the 2014 Chevrolet Spark, the 2014 BMW i3, the 2015 Volkswagen e-Golf, the 2015 BYD e6, the 2017 Nissan LEAF, the 2017 Chevrolet Bolt, and the 2017 Opel Ampera-e.
Together, these models account for about 40 percent of all pure-battery EVs ever produced. In addition to the ten torn-down vehicles, we analyzed publicly available information on additional vehicles and consulted independent subject-matter experts. The resulting analysis shows that successfully producing EVs requires radically different thinking. We identified five key insights:
Want a high-performing electric vehicle? Build a native platform
The benchmarking shows a clear gap in driving range and interior space between models with native EV platforms and those based on ICE. Native EVs optimize battery packaging; non-native EVs force the battery into the awkward footprint of the ICE platform, which limits the realized energy capacity. The native EV battery pack, by contrast, can take a simple, rectangular shape, giving native EVs up to twice the rangeover 300 kilometers per charge and up to approximately 400 kilometers for the best performers, according to the Environmental Protection Agencywithout forcing up the price (Exhibit 1). In addition, native EVs achieve a larger interior space (up to 10 percent by regression line) for the same wheelbase compared with not only non-native counterparts, but also standard ICE vehicles in the same segment.
Theres no convergence yet on core EV powertrain design
The benchmarking included a teardown of the battery, the battery cells, and the thermal-management system. We found three battery-cell designs with different geometries (cylindrical, prismatic, and pouch), along with multiple chemistries. With each design having clear advantages and disadvantages, there is no winner on overall performance for mass-market EVs, as our benchmarking also revealed similar energy density increases of more than 30 percent over a period of seven years (2011 to 2018) across all designs. We also found a large variance in the design approach for thermal management with four battery-cooling solutions: passive (natural air cooling), active combined with powertrain, active but stand-alone dedicated to the battery, and active combined with the air-conditioning circuit. We also identified three archetypes of battery heating: none at all, waste heat from motor and power electronics or the AC system, and dedicated resistive heating integrated in the battery pack. Some dedicated resistive heating units use energy from the battery and work only when the vehicle is charging; others feature a combined liquid cooling/heating cycle using different heat sources, such as resistive heating outside the battery pack (Exhibit 2).
Taking the best performers on the market today, cylindrical cells have the highest energy density with approximately 245 watt-hours per kilogram (Wh/kg), followed by pouch cells with 195 Wh/kgan astounding gap of approximately 25 percent. Prismatic cells have an energy density of approximately 160 Wh/kg. However, the required housing and thermal management evens up the score when looking at the net energy density of the battery pack: 132 Wh/ kg for cylindrical versus 138 Wh/kg for pouch and 104 Wh/kg for prismatic. As there is at present no convergence toward a unique technology or solution, OEMs will still need to invest in these areas to make optimal trade-offs on cost and performance in battery and thermal-management design.
Design to cost has already made its way into EVs
The benchmark reveals that OEMs have startedconsistently applying design to cost (DTC), in particular to the EVs powertrain and body-in-white design, as the battle for performance and range has been won. This trend notably emerges in second-generation EVs. The DTC focus has been mostly on component integration in the powertrain area and smarter usage of lightweight materials in structural parts (Exhibit 3).
Regarding weight, we analyzed major structural components of all ten vehicles to estimate their use of aluminum and composites. Some of the second-generation mass-market EVs use aluminum equal to only 5 to 10 percent of the total vehicle weight on these components, close to the average ICE (approximately 5 percent). In luxury EVs, aluminum accounts for about 40 percent of vehicle weight, mainly to boost acceleration and dynamic performance. Mass-market EVs will continue to converge toward the lower ICE mass-market share of lightweight for three reasons:
- Generational leaps in powertrain technology yield significant weight reductions, which are then directly reinvested into lower-cost structural materials.
- At todays manufacturing cost, batteries, not lightweight materials, are the key to longer ranges.
- EVs lack external incentives for (expensive) weight-reduction measures, which is different from ICEs with their carbon dioxide targets and penalties.
Regarding forthcoming models, the DTC trend will likely continue.
The EV is a radically different vehicleand it needs a radically different offering logic
Automotive OEMs will have to reconceive their business modelto create new income and profit streams for EVs. Today, they rely heavily on customers upgrading the base vehicle with additional engine, transmission, comfort, and safety features, as well as on aftermarket parts and services to boost profitability (and to reach their cost of capital). EVs cost far less to maintain and are far more constrained on options for two reasons (Exhibit 4):
- There is little room for differentiation by performance. Current EVs already offer acceleration comparable to high-specification ICEs in the same segment. Thus, today they offer no more than four combinations of engine and transmission types, compared with the typical 10 to 20 ICE combinations.
- Base EV configurations already contain many options. The high base price of EVs, driven by the cost of the battery, compels OEMs to include more options in the base configuration of an EV than in a comparable ICE, thus losing a high-margin income stream.
Growing supplier offer on major new EV components heavily competes with in-house strategies
- EV powertrains are markedly different from their ICE equivalents in necessary competencies, value add, and component complexity. The growth in EV sales therefore threatens the competitive position and market shares of both OEMs and their ICE-powertrain suppliers.
- Using the supplier logos imprinted on torn-down components in combination with publicly available information, we derived an outside-in view on the OEMs EV-powertrain supply chain. OEMs follow a wide range of strategies when sourcing powertrain components, from almost full vertical integration to nearly full outsourcing. When components are outsourced, the degree of design ownership varies (Exhibit 5).
Given the lower complexity and lower potential for differentiation of most EV-powertrain components, we expect OEMs to outsource a larger share of these components in the future as soon as the design converges to full commodity.
At the same time, we see significant risks for established OEMs and tier-one suppliers. Some tier-one suppliers are already offering a significant share of components outside their original core area. Also, given that EVs are less complex than ICE powertrains, theres greater risk for established OEMs that have strongly differentiated themselves through driving performance. Already, two of todays top five EV manufacturers are new entrants to the EV market: Tesla and BYD.
As demand rises, EV technology and design will continue to evolve, and strategic challenges will follow. Established OEMs and their traditional supplierswill need to rethink their approaches to preserve their revenue and profitability.
Stay current on your favorite topics
Watch Now: Shaping the future: How electric vehicles are driving manufacturing decisions
Updated 24 January 2024 with on-demand video
Shaping the future: how electric vehicles are driving manufacturing decisions on architectures, materials and battery integration
In our latest Premier Livestream, insights were shared by experts from Gestamp and ArcelorMittal on how decisions in electric vehicle design and manufacturing are being influenced by new powertrain layouts and battery integration choices.
The challenges of integrating the battery pack into the vehicle body, particularly in the bodyshop, is adding complexity to the body assembly process. OEMs are aiming to simplify body architectures and battery integration, balancing factors such as light weight, durability, sustainability and cost.
The Livestream looked at key differences in electric vehicle structures, challenges in multi-material bodies, the need for production flexibility in bodyshops, materials, and manufacturing considerations for battery integration, supporting new technologies, sustainability in the design/engineering process, trends in EV architecture, and ongoing developments in the EV design and manufacturing process.
Key points covered:
- OEMs prioritising flexible platforms in EVs for diverse segments and brands
- The current trend where OEMs are looking to simplify body assembly and production optimise efficiency
- Integration of battery packs into vehicle bodies poses challenges, requiring advanced engineering for crash protection systems, which adds cost and complexity to the manufacturing process
- Manufacturers managing elements such as platform design, battery integration methods, and material choices crucial for balancing vehicle bodies for weight, durability, sustainability, and cost
- Market remains highly dynamic, with continuing changes in battery chemistries and configurations, and the potential impact of technologies like hydrogen contributing to an ongoing evolution of EV architectures
Speakers:
Jesse PaegleAutomotive Steel Solution DirectorArcelorMittal
Jessehas worked in the mining and automotive industries since 1997.His experience has given him a good understanding of the entire automotive supply chain and in his current position hesresponsible for steel solutions developments including BIW, Battery pack and chassis components.
Paul BelangerR&D Director North AmericaGestamp
Mr. Belanger leads a team of Body engineers developing products and new technologies from Gestamps North American R&D Center.Paul started his career in the steel industry before moving into automotive with Chryslers Materials Engineering and Ram Truck Body Engineering. Later, at GM, he headed a Manufacturing Engineering team providing expertise with critical stampings and complex assemblies.Mr. Belanger has been using his 30+ years of automotive body and materials engineering experience to drive the development and optimum application of advanced sheet metal products into automotive vehicle production.
Moderator:
With over 20 years experience covering the automotive industry, Nick is responsible for editorial across Automotive Manufacturing Solutions. He has gained wide experience in automotive production operations, visiting OEM and tier supplier factories in Europe, India, China and the US.
Hosted in Partnership With ArcelorMittal
At ArcelorMittal, our goal is to help build a better world with smarter steels. Steels made using innovative processes which are more efficient, use less energy, and emit significantly less carbon. Steels that are cleaner, stronger and reusable. Steels for electric vehicles and renewable energy infrastructure that will support societies as they transform through this century.
We foster this culture of innovation by putting research and development at the heart of our operations.We have some of the best and brightest people in the business engineers who work for us because they get to tackle the most complex of problems.
Upcoming Events
Bringing together automotive designers and engineers, manufacturing engineers and plant leaders the event will delve into the transformative strategies and advancements shaping the future of vehicle design, development, and production.
The second Automotive Evolution North America conference continues to empower manufacturing leaders and experts as they dive deeper into opportunities in localisation, evolving skills, and advanced technologies amid the shift to electrification and sustainability.
Complete the form below to watch the livestream
Future of EV Batteries: Tech, Advancements, & Whats Next
Electric vehicles (EVs) are no longer a distant promise of a sustainable future; they are a reality were living. From increased mileage to decreased emissions, the benefits are astounding. In this blog post, well take you on a deep dive into what truly powers these marvels on wheelsthe battery. Its an essential read for anyone considering making the switch to electric, whether for personal use or as a business move. Before you proceed, if youre still on the fence about EVs, take a minute to check out What Are the Benefits of Electric Cars? to get a fuller picture.
However, EVs have come a long way since their inception. The most remarkable advancements have been in battery technology, a cornerstone for the functioning and efficiency of EVs. If youre in the consideration stage, youre likely asking a lot of questions. How do these batteries work? How long do they last? Are they better than traditional car batteries? Weve got you covered. Consider this your comprehensive guide to EV battery technology. So, buckle up as we explore the power within electric vehicles.
The Evolution of Electric Vehicle (EV) Batteries
The story of the EV battery has its roots in the 19th century, but its in the last two decades that the real magic has happened. Nickel-Metal Hydride (NiMH) batteries were the stars of early electric vehicles. However, they had their limitations, such as lower energy density and reduced life span. Enter Lithium-ion (Li-ion) batteries. These became a game-changer, offering higher energy storage, lower weight, and a longer life cycle.
Teslas Roadster in 2008 set a new benchmark with its lithium-ion cells, offering an unprecedented 245 miles of range. Fast-forward to today, we have EVs that promise more than 400 miles on a single charge. If youre intrigued by the current leaders in this space, dont miss our article on Longest-Range Electric Cars on the Market.
But what does the future hold? Advancements like solid-state batteries and quick charging capabilities are in the pipeline, preparing to usher in a new era of electric driving. Whether youre new to the EV space or considering a transition, understanding the evolution of batteries can provide valuable insight into what youre actually investing in.
What Powers an Electric Car: Understanding the Basics of an EV Battery
In its simplest form, an EV battery is made up of cellssmall units that store energy. These cells are assembled into larger packs to deliver the high voltage required to power an electric vehicle. But how exactly does an EV battery work? Energy is stored in the form of chemical potential in these cells, which is then converted to electrical energy to power the car.
Li-ion batteries are currently the most popular and come in various configurations, each with their own sets of advantages and limitations. For instance, while some may offer quick charging, others may excel in energy density. If youre wondering how to charge these batteries, look no further than our comprehensive guide, How Do You Charge Electric Cars? Everything You Need To Know About EV Charging.
Understanding the basics of an EV battery is like getting to know the heart of the vehicle. With technological strides, were seeing improvements not just in the storage capacities but also in the safety features integrated into these battery systems. Its not just about driving from point A to B anymore; its about doing so in the most efficient, safest way possible.
Breaking Down the Types of EV Batteries
When it comes to electric vehicle batteries, one size does not fit all. There are multiple types of batteries, each with their unique sets of advantages and disadvantages. The two main types youll encounter are Nickel-Metal Hydride (NiMH) and Lithium-ion (Li-ion).
NiMH batteries are older technology but still reliable. Theyre most commonly found in hybrid vehicles and are known for their durability. The downside? Theyre heavier and offer less energy density compared to Li-ion batteries. For the early adopters of electric vehicles, understanding these nuances is crucial.
Li-ion batteries have become the go-to for modern electric vehicles, from Teslas to the latest offerings from traditional automakers. These batteries offer higher energy density, lighter weight, and faster charging capabilities. If youre contemplating a lease or subscription, knowing the type of battery in your chosen vehicle is paramount.
As technology continues to evolve, were also seeing exciting developments in solid-state batteries, which promise even higher energy density and faster charging times. But for now, Li-ion remains the top choice for anyone looking for efficiency and performance in an electric vehicle.

How Battery Technology is Changing the Game: Advancements in Battery Life
The battery life of electric vehicles has been a point of concern for potential buyers for years. However, advancements in technology are pushing these limits further than ever before. Were now seeing EVs capable of more than 400 miles on a single charge. With improvements in energy density and thermal management, your battery not only lasts longer but performs more efficiently. For more insights on the revolutionary advances in this area, check out our article Top Revolutionary Advances in EV Battery Technology.
Companies are pouring billions into R&D to further optimize the life cycle of these batteries, aiming for quicker charging and longer durability. These advancements have begun trickling down from premium models to more affordable options, making long-lasting batteries accessible to the mass market.
The future is even more promising. With research into new materials and configurations, we might soon have batteries that last for a million miles. Yes, you read that righta million miles!
What to Look for in an EV Battery: A Buyers Checklist
If youre in the market for an electric vehicle, understanding the battery is crucial. Here are a few key points to consider:
- Energy Density: How much energy can the battery store? The higher the energy density, the longer the range.
- Longevity: How long will the battery last? Manufacturers usually offer warranties, but its essential to read the fine print.
- Charge Time: How quickly can the battery be fully charged? Nobody wants to spend hours waiting.
- Cost: Batteries can be expensive to replace. Ensure you know the replacement cost and the warranty details.
- Safety Features: Look for thermal management and other built-in safety features.
In a nutshell, the ideal battery balances performance, longevity, and safety. To help you make an informed decision, our article Revolutionizing Car Ownership: The Car Subscription Model goes into detail about how a subscription model like Steer EV can help you test different electric vehicles and their batteries without a long-term commitment.
The Future Prospects: Whats Next in EV Battery Technology?
Electric vehicles are hitting the mainstream, but the technology powering them is far from stagnant. Were on the cusp of even greater innovations that promise to revolutionize the EV landscape. For starters, solid-state batteries are emerging as the next big thing. These batteries promise quicker charging times and even longer life, positioning them as potential game-changers. Want to be part of the revolution? Our article Facedrive to Launch Steer EV Subscription Service Platform in Toronto covers how you can get onboard with cutting-edge EVs right here in Toronto.
Another intriguing development is the exploration of new materials. Scientists are looking beyond lithium to other materials like silicon or even air. The aim? To create batteries that are not just more efficient but also more eco-friendly. If youre interested in the environmental benefits of EVs, dont miss our post The Environmental Impact of Electric Cars: A Comparison to Gas-Powered Cars.
Also, lets not overlook wireless charging and innovations in regenerative braking. These advancements are poised to make electric vehicles more convenient and energy-efficient. With so much on the horizon, the future of EVs looks brighter than ever.
Conclusion
The realm of electric vehicles is evolving at a breakneck speed, and at the heart of this revolution is battery technology. From understanding the types of batteries and their advancements to foreseeing future prospects, its clear that EV batteries are redefining the rules of the game. As you consider stepping into the world of electric vehicles, make sure youre up-to-date with the latest trends and technologies. Our article What is a Car Subscription? The Ultimate Beginners Guide is a great starting point to understand how a car subscription model can offer you the flexibility to adapt as technology advances. Its an exciting time to be an EV enthusiast, and were thrilled youre taking this electrifying journey with us!
Tags: